Introduction
Diesel generators play a crucial role in providing backup power during outages or in remote locations where grid power is not accessible. These generators are relied upon in various industries, including healthcare, data centers, manufacturing, and telecommunications, to ensure continuous operations. However, the performance and reliability of diesel generators can be affected by various factors such as wear and tear, improper maintenance, and environmental conditions. To address these challenges and ensure optimal performance, condition monitoring of diesel generators has become essential.
This article explores the importance of condition monitoring for diesel generators, the key parameters to monitor, various techniques and technologies available for monitoring, and the benefits of implementing a robust condition monitoring program.
Importance of Condition Monitoring for Diesel Generators
Condition monitoring involves the continuous monitoring of key parameters and performance indicators of a machine or equipment to detect any deviations from normal operating conditions. For diesel generators, condition monitoring is crucial for several reasons:
1. Early Detection of Problems: By monitoring key parameters such as temperature, vibration, oil quality, and fuel consumption, potential issues can be detected early before they escalate into major failures. This proactive approach helps in avoiding costly downtime and repairs.
2. Improved Reliability: Regular monitoring and analysis of generator performance can help in identifying trends and patterns that indicate the overall health of the equipment. By addressing minor issues promptly, the reliability and lifespan of the diesel generator can be improved.
3. Optimal Performance: Condition monitoring allows operators to optimize the operation of diesel generators by ensuring that they are running at peak efficiency. By adjusting parameters based on real-time data, fuel consumption can be optimized, and unnecessary wear and tear can be minimized.
4. Safety: Monitoring critical parameters such as temperature and oil pressure can help in ensuring the safe operation of diesel generators. Abnormal readings can indicate potential safety hazards, allowing operators to take corrective action before an incident occurs.
Key Parameters to Monitor
Several key parameters should be monitored to ensure the effective condition monitoring of diesel generators. These parameters provide valuable insights into the performance, health, and efficiency of the equipment. Some of the key parameters include:
1. Oil Quality: Monitoring the quality and condition of the lubricating oil is essential for diesel generators. Contaminated or degraded oil can lead to increased friction, wear on components, and reduced efficiency. Regular oil analysis can help in detecting issues such as contamination, oxidation, and viscosity changes.
2. 150kw diesel generator : Monitoring the temperature of critical components such as the engine, alternator, and cooling system is vital for detecting overheating issues. High temperatures can lead to accelerated wear, reduced efficiency, and potential failures. Continuous temperature monitoring can help in identifying cooling system problems or inadequate ventilation.
3. Vibration Levels: Excessive vibration can indicate misalignment, worn bearings, unbalanced components, or other mechanical issues. Monitoring vibration levels can help in detecting these issues early and preventing catastrophic failures. Vibration analysis can also provide valuable insights into the condition of rotating machinery.
4. Fuel Consumption: Monitoring fuel consumption can help in assessing the efficiency of diesel generators. Sudden increases in fuel consumption can indicate issues such as fuel leaks, inefficient combustion, or engine malfunctions. By tracking fuel consumption trends, operators can optimize the performance of the generator and reduce operating costs.
5. Battery Health: The condition of the batteries is crucial for the reliable operation of diesel generators. Monitoring parameters such as voltage, charge level, and internal resistance can help in ensuring that the batteries are in good condition and capable of providing backup power when needed.
Techniques and Technologies for Condition Monitoring
Several techniques and technologies are available for condition monitoring of diesel generators. These techniques vary in complexity, cost, and effectiveness, and can be used individually or in combination to create a comprehensive monitoring program. Some of the common techniques and technologies include:
1. Remote Monitoring Systems: Remote monitoring systems allow operators to track key parameters and performance indicators of diesel generators in real-time from a central location. These systems use sensors, data acquisition units, and communication networks to collect and transmit data for analysis. Remote monitoring systems provide visibility into the health and status of the generator, enabling proactive maintenance and troubleshooting.
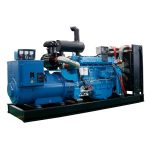
2. Oil Analysis: Oil analysis involves sampling and testing the lubricating oil of diesel generators to assess its condition and identify potential issues. Oil analysis can detect contaminants, wear particles, fuel dilution, and other indicators of engine health. By analyzing oil samples regularly, operators can monitor the condition of the engine and make informed maintenance decisions.
3. Vibration Analysis: Vibration analysis is a powerful tool for monitoring the mechanical condition of diesel generators. By measuring and analyzing vibration levels using accelerometers and vibration analysis software, operators can detect abnormalities in rotating machinery, such as misalignment, imbalance, or bearing wear. Vibration analysis can help in predicting potential failures and scheduling maintenance proactively.
4. Thermal Imaging: Thermal imaging cameras can be used to monitor the temperature of critical components of diesel generators. By capturing infrared images of the equipment, operators can identify hotspots, overheating issues, and thermal anomalies that may indicate pending failures. Thermal imaging can help in diagnosing cooling system problems, electrical faults, and insulation issues.
5. Condition-Based Maintenance (CBM): Condition-based maintenance is a strategy that relies on monitoring the condition of equipment to determine the optimal time for maintenance activities. By using data from various monitoring techniques, CBM allows operators to schedule maintenance based on the actual condition of the equipment rather than a predefined schedule. This approach can help in maximizing equipment uptime, reducing maintenance costs, and extending the lifespan of diesel generators.
Benefits of Implementing a Robust Condition Monitoring Program
Implementing a robust condition monitoring program for diesel generators offers several benefits to operators and organizations. Some of the key benefits include:
1. Increased Reliability: By monitoring key parameters and performance indicators, operators can identify potential issues early and take corrective actions to prevent failures. This proactive approach helps in increasing the reliability of diesel generators and reducing unplanned downtime.
2. Extended Equipment Lifespan: Regular monitoring and maintenance based on actual equipment condition can help in extending the lifespan of diesel generators. By addressing issues promptly and optimizing performance, operators can avoid premature failures and costly replacements.
3. Cost Savings: Condition monitoring can help in reducing maintenance costs by enabling predictive maintenance rather than reactive repairs. By identifying issues before they escalate, operators can schedule maintenance activities more efficiently, use resources effectively, and minimize downtime-related expenses.
4. Improved Safety: Monitoring critical parameters such as temperature, vibration, and fuel consumption can help in ensuring the safe operation of diesel generators. By detecting potential safety hazards early, operators can prevent accidents, injuries, and equipment damage.
5. Enhanced Operational Efficiency: Condition monitoring allows operators to optimize the performance of diesel generators by adjusting parameters based on real-time data. By running the equipment at peak efficiency, operators can reduce fuel consumption, minimize wear and tear, and improve overall operational efficiency.
Conclusion
Condition monitoring of diesel generators is essential for ensuring the reliability, performance, and safety of these critical assets. By monitoring key parameters such as oil quality, temperature, vibration, fuel consumption, and battery health, operators can detect issues early and take proactive measures to prevent failures. Various techniques and technologies such as remote monitoring systems, oil analysis, vibration analysis, thermal imaging, and condition-based maintenance can be used to create a comprehensive monitoring program.
Implementing a robust condition monitoring program offers numerous benefits, including increased reliability, extended equipment lifespan, cost savings, improved safety, and enhanced operational efficiency. By investing in condition monitoring and adopting a proactive maintenance approach, operators can optimize the performance of diesel generators, minimize downtime, and maximize the return on investment in these critical assets.